Grenfell Tower in London was covered in flammable materials because of “systematic dishonesty” from those who made and sold cladding and insulation, the final report has concluded.
Here is a summary of the main firms and what the inquiry into the disaster said about them.
Kingspan
The Irish company has long said its K15 insulation product made up 5 per cent of the insulation in the tower block and was used without its knowledge.
But the report found that Kingspan “knowingly” created a “false market in insulation” from 2005 onwards for use on buildings over 18 metres tall by claiming its K15 product had been part of a system that had been successfully tested under the BS 8414 cladding fire safety test, meaning it could be used in the wall of any building of that height regardless of its design or other components.
The inquiry branded this a “false claim”, adding: “As Kingspan knew, K15 could not honestly be sold as suitable for use in the external walls of buildings over 18 metres in height generally, but that is what it had succeeded in doing for many years.”
Kingspan relied on the results of a single cladding fire safety test performed in 2005, on a system whose components were not representative of a typical external wall, the report said, and found that the firm continued to rely on that test despite changing the composition of K15 in 2006.
Further tests on systems incorporating K15 in the following two years were “disastrous”, the report said, but Kingspan did not withdraw the product from the market, “despite its own concerns about its fire performance”.
In 2009, Kingspan obtained a certificate that “contained false statements about K15”, the report said, and on which it relied “for many years to sell the product”, adding that it made a “calculated decision” to use the certificate to “mask, or distract from, the absence of supporting test evidence”.
The report said Kingspan “cynically exploited” the industry’s lack of detailed knowledge about insulation and cladding fire safety tests, and “relied on the fact that an unsuspecting market was very likely to rely on its own claim about the product”.
Responding to the report, Kingspan said it had “long acknowledged the wholly unacceptable historical failings that occurred in part of our UK insulation business” but said these were “in no way reflective of how we conduct ourselves as a group, then or now”.
It said it remains “committed to playing a leading role in providing safe and sustainable building solutions, including continuing to work with government and industry partners”.
Arconic
Arconic Architectural Products made and sold the Reynobond 55 cladding panels with a polyethylene (PE) core which were used in the refurbishment of Grenfell Tower and were later found to have fuelled the blaze.
The phase one report in 2019 concluded the “principal reason” the flames shot up the building at such speed was the combustible cladding, which acted as a “source of fuel”.
The final report noted that polyethylene “burns fiercely” and, when used in cassette form (as in three-dimensional structures), the Reynobond 55 PE was “extremely dangerous”.
The phase two report stated that, from 2005 until after the Grenfell Tower fire, Arconic “deliberately concealed from the market the true extent of the danger of using Reynobond 55 in cassette form, particularly on high-rise buildings”.
By summer 2011, Arconic was “well aware that Reynobond 55 PE cassette form performed much worse in a fire and was considerably more dangerous than in riveted form” but was “determined to exploit what it saw as weak regulatory regimes in certain countries (including the UK) to sell it in cassette form “including for use on residential buildings”.
Even after cladding fires in Dubai in 2012 and 2013, Arconic did not consider withdrawing the product in favour of the fire-resistant version, instead “it allowed customers in the UK to continue buying the unmodified product, giving them to understand that it would tell them if it was unsuitable for the use to which they intended to put it, although without any intention of doing so”.
Further testing in 2013 saw Arconic decide Reynobond 55 PE would be certified as Class E only – which deems a product to be combustible and only able to resist a small flame for a few seconds – whether used in either riveted or cassette form.
It did not pass that information on to its customers in the UK, a move the inquiry deemed as “not an oversight”, adding: “It reflected a deliberate strategy to continue selling Reynobond 55 PE in the UK based on a statement about its fire performance that it knew to be false.”
Responding to the inquiry, Arconic said it was its subsidiary, Arconic Architectural Products SAS (AAP), which had supplied the material used for cladding in the tower’s refurbishment, and that it rejects “any claim that AAP sold an unsafe product” and “did not conceal information from or mislead any certification body, customer, or the public”.
Celotex
Celotex was the manufacturer of the majority of the insulation boards used in the refurbishment.
Its Rs5000 was one of the insulation components used in the Grenfell Tower rainscreen cladding system and its TB4000 insulation was used to fill gaps in the window surrounds during the refurbishment of the tower.
The inquiry’s final report concluded that it had “embarked on a dishonest scheme to mislead its customers and the wider market” in an attempt to break into a market which had been dominated by Kingspan.
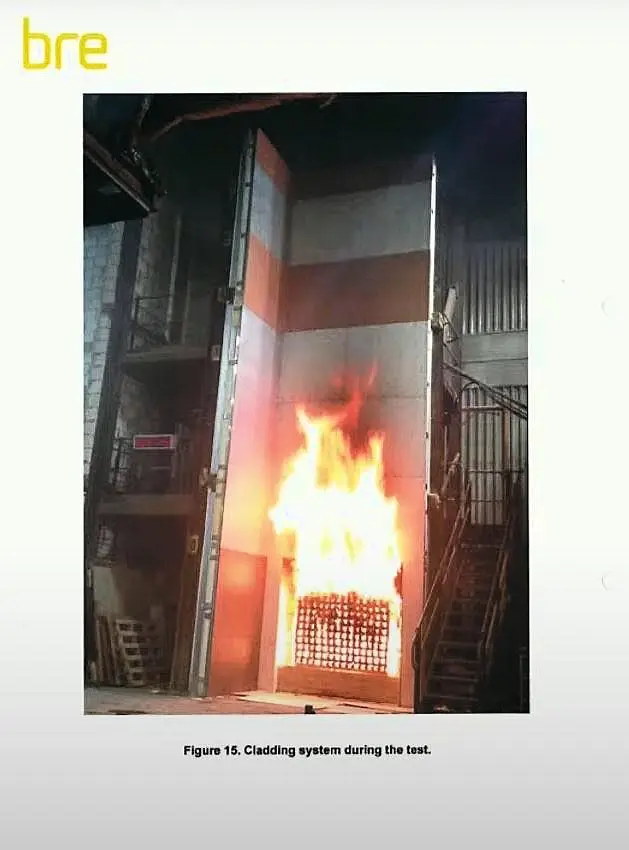
In 2014 Celotex tested “with the complicity of BRE (Building Research Establishment)” a system incorporating RS5000 which contained “two sets of fire-resistant magnesium oxide boards placed in critical positions to ensure that it passed”.
A test report “omitted any reference to the magnesium oxide boards, thereby rendering it materially incomplete and misleading” and the product was marketed as the first to meet that test and as “acceptable for use in buildings above 18 metres in height”.
But the test Celotex relied on to support this claim “had been manipulated as we have described above, a fact that Celotex did not disclose in its marketing literature”.
The system test did not involve the testing or classification of individual products, something Celotex had “deliberately” tucked away “in the small print of its marketing literature”, the report said.
In its response, Celotex said it had “reviewed and improved process controls, quality management and the approach to marketing within the Celotex business to meet industry best practice”.
Rydon
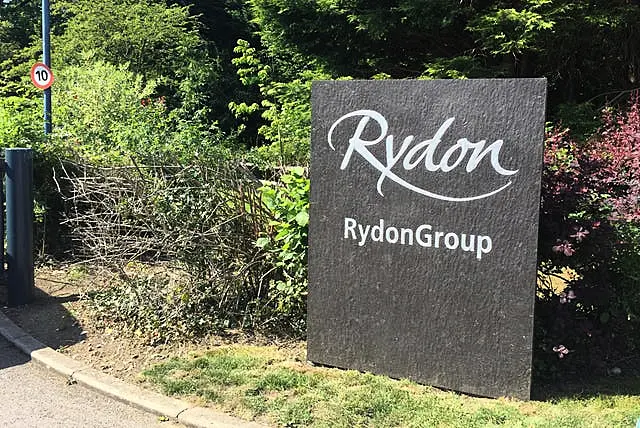
Rydon was appointed in 2014 as the design and build contractor for the refurbishment of Grenfell Tower.
Along with architect Studio E it was deemed to have taken “a casual approach to contractual relations”.
The report said Rydon “saw its role as as little more than the conductor of a large and varied orchestra”, and had not employed anyone with the “knowledge and skills required to design or carry out the refurbishment”.
The report found Rydon was “ill-equipped to oversee the work of its sub-contractors and consultants” and that the firm and others appeared to have “assumed that someone else was, or should be, taking responsibility for critical decisions, such as the choice of insulation, rainscreen panels and other materials”.
Studio E
Architect Studio E was responsible for the design of the external wall and the choice of materials used in the construction.
Its “failure to recognise” the ACM (aluminium composite material) was dangerous and to warn the tenant management organisation (TMO) against using it “represented a failure to act in accordance with the standard of a reasonably competent architect”.
Its failure also to recognise that the Celotex insulation was combustible and unsuitable for use in a high-rise meant it “bears a very significant degree of responsibility for the disaster”.
BRE
The Building Research Establishment had, the report noted, held a trusted position within the construction industry and was recognised both nationally and internationally as a leader in fire safety.
But it added: “However, from 1991 much of the work it carried out in relation to testing the fire safety of external walls was marred by unprofessional conduct, inadequate practices, a lack of effective oversight, poor reporting and a lack of scientific rigour.”
It had been a British government agency providing independent advice and information on building performance, construction and fire safety in the UK, before it was privatised in 1997.
Senior BRE staff gave advice to customers including Kingspan and Celotex, the inquiry said, on the best way to satisfy the criteria for a system to be considered safe, “thereby compromising its integrity and independence”.
The report said that in some cases there was “evidence of a desire to accommodate existing customers and to retain its status within the industry at the expense of maintaining the rigour of its processes and considerations of public safety”.
Exova
Exova provided fire safety advice to Kensington and Chelsea Tenant Management Organisation (KCTMO) for the proposed tower refurbishment.
The final report found that Exova “bears considerable responsibility for the fact that Grenfell Tower was in a dangerous condition on completion of the refurbishment”.
The “most serious criticism” it said, was that Exova “failed to produce a final version of the fire safety strategy” for the refurbished building and had “failed” to warn the design team about the potential consequences of that.
It stated: “Exova’s attitude was wholly inconsistent with the careful approach to matters affecting the safety of life to be expected of a reasonably competent fire engineer.”